Sample costs and returns to establish and produce bulb onions under drip/set spot irrigation in Northwestern Nevada are presented in this publication. This publication is intended to be a guide, used to make production decisions, determine potential returns, and prepare business and marketing plans. Practices described are based on the production practices considered typical for this crop and region, but may not apply to every situation. The “Your Farm” column in Table 1 is provided for your use.
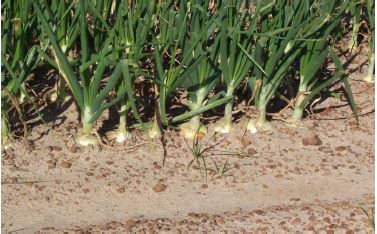
Assumptions
The following assumptions refer to Tables 1 through 4 and reflect the typical costs and returns to produce bulb onions under drip/set spot irrigation in Northwestern Nevada. The practices described are not the recommendations of the University of Nevada, Reno, but rather the production practices and materials considered typical of a well-managed farm in the region, as determined by a producer panel in October 2007. Costs, materials and practices are not applicable to all situations because establishment and cultural practices vary among growers within the region.
Farm
The representative farm consists of 450 acres of land, on which 200 acres are cultivated for white or red onion production, 200 acres are cultivated for yellow onion production, and 50 acres are used for owner housing, refrigeration, storage, packing, and roads. The representative farm is part of a larger operation, as onions should not be grown in the same plots for more than two years. During the growing season the enterprise will produce one harvest with total production at 1500 to 1800 50wt bags per acre. The minimum land market value in 2008 was approximately $11,500.00 per acre for agricultural land in northwestern Nevada with water rights.
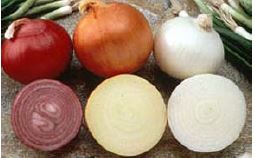
Production Cultural Practices and Material Inputs
Land Preparation
Onions are frequently grown on plots where alfalfa was the previous crop. In September, two quarts per acre of Roundup* are applied to kill any remaining alfalfa residue. In mid-September, the field is disked three times with a light offset disk and once with a heavy offset disk. The ground is ripped with both a deep and a finish ripper to break up the soil to improve water infiltration and fertilizer penetration. After another pass with the heavy offset disk, the field is planed twice to remove small high and low spots. Three tons of gypsum per acre (at $396.00/acre) and one-half ton of sulfuric acid per acre (at $100.00/acre) are applied as soil amendments, along with 100 lbs. per acre of both phosphorus and potash and 50 lbs. per acre of nitrogen (at $173.00/acre). Rows are pulled with a lister and the beds are pre-shaped with a bed shaper. Portable pumps with diesel engines and fuel tanks are placed alongside ditches. The pump end is situated in the ditch and a solid set of sprinkler lines are placed in the furrows and remain there during the growing season. Set spot sprinklers act as a conveyance for weekly application of liquid fungicides, bactericides, insecticides, and fertilizers in addition to providing supplemental irrigation. Ten days following an initial preirrigation of two inches of water, Vapam* (at $142.00/acre) is applied through the set sprinklers as an herbicide and fungicide with two inches of water. Winter wheat is planted as a cover crop in October thirty days after the Vapam* application. An additional four inches of water will be applied to the fields in the late fall to establish the winter wheat crop. After the winter wheat is sprayed out with Fusilade* (at $30.00/acre) in early April, the beds are aerated and shaped. After shaping, a pop-up fertilizer (7.5-26-05 at $50.00/acre) is applied. Drip tape is installed sub-surface so that the water is delivered 2 to 3 inches below the roots.
Planting
In mid-April, onion seed is planted with a vacuum planter at 250,000 seeds per acre.
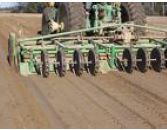
Irrigation
Irrigation begins in April and continues through until the first of August. Irrigation occurs every three days through the buried drip tape and weekly through the set spot sprinklers. Irrigation costs shown in Table 1 cover the per acre cost of water at $25.00 per acre foot, plus an administration fee of $50.00 per land parcel, which is assumed to be one parcel per every 50 acres, or eight for the 400 acre farm. Maintenance costs on ditches, such as hauling dirt to fix wash-outs, broken head gates and machinery costs to weed the ditches are $400.00 annually. Material costs for the drip tape itself are $500.00 per acre; filters and other necessary parts cost $240.00 per acre and have a five year life for a per acre per year cost of $48.00. Diesel for the portable pumps is an additional $64.00 an acre. Total irrigation costs excluding labor are $698.00 per acre and include the eight inches applied to the winter wheat cover crop.
Fertilization
Commercial fertilizer (32-0-0* at $45.00/acre) is applied through the set spot sprinklers in May.
Pest Management
A variety of pest management methods are used depending on pest population cycles. Pest treatment will normally begin in April and continue for the five month production cycle. Tissue sampling is done monthly as a check against infestation.
Weeds
Herbicides commonly used are Goal* and Prowl*. A combination of two or more is common at an annual per-acre cost of $77.65. In addition to chemical treatment, the beds are hand-weeded once a season.
Insects
Thrips and onion maggot are the primary insect threats to onions; however aphids, leaf miners, mites, seed corn maggots, and armyworms can also pose problems. These insects are a constant threat. Therefore, insecticide is applied weekly during the growing season by the set spot sprinklers. The total price for insect control is $68.05 per acre.
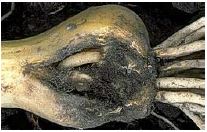
Disease
Downy mildew, rust and purple blotch are common disease problems in onion stands. Several types of bacterial rots are another major threat. Fungicides and bactericides are common treatments at an annual per-acre rate of $213.00.
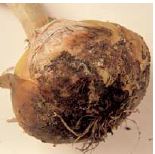
Harvest
Prior to harvest, irrigation is stopped and the set spot sprinkler lines are pulled from the field. A coulter and shank are run to open the furrows. Rod lifters are used to undercut the roots, loosening the onions. The onion tops and roots are then hand clipped and the bulbs are placed in 125 pound burlap bags and left to air dry or cure in the field for ten days. Harvest equipment owned by the farm and operated by the owner/operator or hired help consists of a coulter and shank, a rod lifter, and two sack loaders pulled by tractors to haul the onions off the field. After the onions are removed, a winder is rented to remove the drip tape which is then recycled.
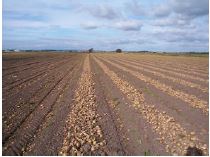
Labor
The owner/operator wage is based on an allowance to the owner/operator of $75.00 per acre. Hired labor for the 400 acre farm is $800,000. All employee benefits, payroll taxes and worker’s compensation insurance are included in labor costs. Employee housing and associated utilities are included in the farm investment costs.
Utilities
Current utilities rates calculated using information from Nevada Power and SWGAS Base utility costs of $350 per month for the household were combined with costs of $7 per acre per year to allow for utilities for outbuildings and shops.
Yield
The 400 acre farm yields 660,000 50 wt bags of red, white, and yellow onions.
Processing
The onions, after being removed from the field, are trucked to storage buildings and stacked with a piler, where they will be heated to a temperature of 96oF for two weeks by propane heat for additional drying. They will then be cooled and moved to a storage location until they can be packed and shipped. Approximately ten percent of the harvest will be processed immediately; fifteen percent will go to a ventilated building and will be packed next; seventy-five percent of the harvest will go to a refrigerated building until it can be packed and shipped.
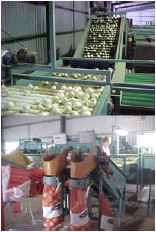
Packing
Packing occurs from harvest through March of the following year. The onions are graded using a sorter and bagged in consumer packs of 2-3 pounds or in 50 pound mesh bags. Packing equipment owned by the farm consists of a sorter, three large baggers for the 50 lb. bags, a small bagger for the consumer packs, a skid steerloader, and two forklifts.
Returns
Returns are based on 2007 market prices across a range of onion quality levels. An estimated price of $8.00 per 50 lb. bag of white or red onions, and $4.00 per 50 lb. bag of yellow onions was used to calculate returns. Returns will vary during the growing season due to market conditions.
Overhead and Capital Recovery Costs
Cash Overhead
Cash overhead consists of various cash expenses paid out during the year. These costs include property taxes, interest, office expenses, liability and property insurance, as well as investment/machinery repairs. A complete listing of farm investments and associated costs can be found in Table 2.
Interest on Operating Capital
Total operating capital is calculated based on 80 percent of total operating (variable) costs. The interest on operating capital is calculated at a rate of 6.5 percent for the six month production cycle.
Property Taxes
Property taxes in Nevada differ across counties. For the purposes of this publication, investment property taxes are calculated at 1 percent of the average asset value of the property.
Insurance
Insurance on farm investments vary, depending on the assets included and the amount of coverage. Property insurance provides coverage for property loss at .666 percent of the average asset value. Liability insurance covers accidents on the farm at an annual cost of $1,749.00. Insurance information provided by Kevin Ogan of Beauchamp & McSpadden, Inc.
Fuel and Lube
The fuel and lube for each piece of equipment is calculated at 8 percent of the purchase price.
Investment Repairs
Annual repairs on all farm investments or capital recovery items that require maintenance are calculated at 2 percent of the purchase price for buildings, improvements, and equipment and 7 percent of the purchase price for machinery and vehicles.
Office & Travel
Office and travel costs are estimated at $3,000.00 for an average year. These expenses include office supplies, telephone service, Internet service, and travel expenses to educational seminars.
Capital Recovery
Capital recovery costs are the annual depreciation (opportunity cost) of all farm investments. Capital recovery costs are calculated using straight line depreciation. Farm equipment may be purchased new or used depending on producer panel preferences.
Salvage Value
Salvage value is 10 percent of the new purchase price, which is an estimate of the remaining value of an investment at the end of its useful life. The salvage value for land is the purchase price, as land does not normally depreciate.
Average Asset Value Computation
(Purchase Price + Salvage Value divided by 2)
Straight Line Depreciation Computation
(Purchase Price - Salvage Value divided by Useful Life)
*The information given herein is supplied with the understanding that no discrimination is intended and no endorsement by Cooperative Extension is implied.
REFERENCES
- Nevada Power (2008). Current pricing for agricultural properties with water rights in northwestern Nevada.
- Smathers, Robert (2007). The Costs of Owning and Operating Farm Machinery in the Pacific Northwest 2005. A Pacific Northwest Publication #346. University of Idaho, Washington State University, and Oregon State University.
NOTES
Sample production costs and returns publications for significant agricultural products in various regions of Nevada are available online at the University of Nevada Cooperative Extension Web site at UNCE. For additional information, contact the Department of Resource Economics at the University of Nevada, Reno at (775) 784-6701 or your local University of Nevada Cooperative Extension office.
Table 1: Northwestern Nevada Onion Production Costs & Returns, 400 acres, 2008
Gross Income |
Total Units |
Unit |
Price/Cost Per Unit |
Total Cost/Value |
Total Cost/Value Per Acre |
Your Farm |
White or Red Onions |
1500.00 |
50wt |
$8.00 |
$2,400,000.00 |
$6,000.00 |
|
Yellow Onions |
1800.00 |
50wt |
$4.50 |
$1,620,000.00 |
$4,050.00 |
|
Total Gross Income |
|
|
|
$4,020,000.00 |
$10,050.00 |
|
Operating Costs |
Total Units |
Unit |
Price/Cost Per Unit |
Total Cost/Value |
Total Cost/Value Per Acre |
Your Farm |
Roundup Application (Custom) |
400.00 |
Acre |
$5.00 |
$2,000.00 |
$5.00 |
|
Pre-plant Fertilizer Application (Custom) |
400.00 |
Acre |
$25.00 |
$10,000.00 |
$25.00 |
|
Listing (Custom) |
400.00 |
Acre |
$25.00 |
$10,000.00 |
$25.00 |
|
Seed |
400.00 |
Acre |
$375.00 |
$150,000.00 |
$375.00 |
|
Fungicide & Bactericide |
400.00 |
Acre |
$213.00 |
$85,200.00 |
$213.00 |
|
Insecticide |
400.00 |
Acre |
$210.05 |
$84,020.00 |
$210.05 |
|
Herbicide |
400.00 |
Acre |
$107.65 |
$43,060.00 |
$107.65 |
|
Fertilizer |
400.00 |
Acre |
$754.00 |
$301,600.00 |
$754.00 |
|
Irrigation |
400.00 |
Acre |
$698.00 |
$279,200.00 |
$698.00 |
|
Hired Labor |
400.00 |
Acre |
$2,000.00 |
$800,000.00 |
$2,000.00 |
|
Harvesting |
660000.00 |
50wt |
$0.25 |
$165,000.00 |
$412.50 |
|
Trucking |
660000.00 |
50wt |
$0.25 |
$165,000.00 |
$412.50 |
|
Drying |
660000.00 |
50wt |
$0.15 |
$99,000.00 |
$247.50 |
|
Ventilation |
99000.00 |
50wt |
$0.04 |
$3,960.00 |
$9.90 |
|
Refrigeration |
495000.00 |
50wt |
$2.10 |
$173,250.00 |
$433.13 |
|
Packing + Bags |
660000.00 |
50wt |
$1.05 |
$693,000.00 |
$1,732.50 |
|
Operator Labor |
400.00 |
Acre |
$75.00 |
$30,000.00 |
$75.00 |
|
Accounting & Legal |
1.00 |
Annual |
$2,000.00 |
$2,000.00 |
$5.00 |
|
Fuel & Lube |
1.00 |
Annual |
$118,587.12 |
$118,587.12 |
$296.47 |
|
Maintenance |
1.00 |
Annual |
$180,050.34 |
$180,050.34 |
$450.13 |
|
Utilities |
1.00 |
Annual |
$7,000.00 |
$7,000.00 |
$17.50 |
|
Miscellaneous |
400.00 |
Acre |
$5.00 |
$2,000.00 |
$5.00 |
|
Operating Capital Interest |
$2,723,141.97 |
$ |
$0.065 |
$88,502.11 |
$221.26 |
|
Total Operating Costs |
|
|
|
$3,492,429.57 |
$8,731.07 |
|
Income Above Operating Costs |
|
|
|
$527,570.43 |
$1,318.93 |
|
Ownership & Cash Overhead Costs |
Total Cost/Value |
Total Cost/Value Per Acre |
Your Farm |
Liability Insurance |
$1,749.00 |
$4.37 |
|
Office & Travel |
$3,000.00 |
$7.50 |
|
Annual Investment Insurance |
$20,001.10 |
$50.00 |
|
Annual Investment Taxes |
$81,781.68 |
$204.45 |
|
Total Cash Overhead Costs |
$106,531.78 |
$266.33 |
|
Noncash Overhead Costs (Capital Recovery) |
Total Cost/Value |
Total Cost/Value Per Acre |
Your Farm |
Buildings, Improvements, & Equipment |
$304,819.83 |
$762.05 |
|
Machinery & Vehicles |
$100,155.42 |
$250.39 |
|
Total Noncash Overhead Costs |
$404,975.25 |
$1,012.44 |
|
Total Ownership Costs |
$511,507.03 |
$1,278.77 |
|
Total Costs |
$4,003,936.61 |
$10,009.84 |
|
Net Projected Returns |
$16,063.39 |
$40.16 |
|
Table 2: Investment Summary
Buildings, Improvements, and Equipment |
Purchase Price |
Useful Life (Yrs) |
Salvage Value |
Annual Capital Recovery |
Annual Insurance |
Annual Taxes |
Annual Repairs |
Owner House |
$200,000.00 |
50.00 |
$200,000.00 |
- |
$1,332.00 |
$2,000.00 |
$4,000.00 |
Land |
$5,175,000.00 |
150.00 |
$5,175,000.00 |
- |
- |
$51,750.00 |
- |
Shop (30X40) & Tools |
$36,000.00 |
25.00 |
$3,600.00 |
$1,296.00 |
$131.87 |
$198.00 |
$720.00 |
Metal Equipment Shed (20X80) |
$24,000.00 |
25.00 |
$2,400.00 |
$864.00 |
$87.91 |
$132.00 |
$480.00 |
Implements |
$154,330.50 |
15.00 |
$15,433.05 |
$9,259.83 |
$565.31 |
$848.82 |
$3,086.61 |
Refrigerated Building |
$1,300,000.00 |
20.00 |
$130,000.00 |
$58,500.00 |
$4,761.90 |
$7,150.00 |
$26,000.00 |
Storage and Packing Buildings (4) |
$1,200,000.00 |
25.00 |
$120,000.00 |
$43,200.00 |
$4,395.60 |
$6,600.00 |
$24,000.00 |
Burlap Bags |
$250,800.00 |
4.00 |
- |
$62,700.00 |
- |
- |
- |
Solid Set Sprinkler System |
$800,000.00 |
6.00 |
$80,000.00 |
$120,000.00 |
$2,930.40 |
$4,400.00 |
$16,000.00 |
Filtration System for Drip |
$100,000.00 |
10.00 |
$10,000.00 |
$9,000.00 |
$366.30 |
$550.00 |
$2,000.00 |
Sub Total |
$9,240,130.50 |
NA |
$5,736,433.05 |
$304,819.83 |
$14,571.29 |
$73,628.82 |
$76,286.61 |
Machinery and Vehicles |
Purchase Price |
Useful Life (Yrs) |
Salvage Value |
Annual Capital Recovery |
Annual Insurance |
Annual Taxes |
Annual Repairs |
Annual Fuel & Lube |
385 HP Tractor |
$243,856.00 |
15.00 |
$24,385.60 |
$14,631.36 |
$893.24 |
$1,341.21 |
$17,069.92 |
$19,508.48 |
255 HP Tractor |
$208,182.00 |
15.00 |
$20,818.20 |
$12,490.92 |
$762.57 |
$1,145.00 |
$14,572.74 |
$16,654.56 |
150 HP Tractor |
$123,965.00 |
15.00 |
$12,396.50 |
$7,437.90 |
$454.08 |
$681.81 |
$8,677.55 |
$9,917.20 |
Piler (used) |
$40,000.00 |
15.00 |
$4,000.00 |
$2,400.00 |
$146.52 |
$220.00 |
$2,800.00 |
$3,200.00 |
Sack Loader (2) |
$88,836.00 |
10.00 |
$8,883.60 |
$7,995.24 |
$325.41 |
$488.60 |
$6,218.52 |
$7,106.88 |
Sorter |
$300,000.00 |
15.00 |
$30,000.00 |
$18,000.00 |
$1,098.90 |
$1,650.00 |
$21,000.00 |
$24,000.00 |
Skid Steer loader |
$22,500.00 |
10.00 |
$2,250.00 |
$2,025.00 |
$82.42 |
$123.75 |
$1,575.00 |
$1,800.00 |
Baggers (4) |
$245,000.00 |
15.00 |
$24,500.00 |
$14,700.00 |
$897.44 |
$1,347.50 |
$17,150.00 |
$19,600.00 |
Forklift (2) |
$60,000.00 |
15.00 |
$6,000.00 |
$3,600.00 |
$219.78 |
$330.00 |
$4,200.00 |
$4,800.00 |
1 Ton Pickup (3) |
$150,000.00 |
8.00 |
$15,000.00 |
$16,875.00 |
$549.45 |
$825.00 |
$10,500.00 |
$12,000.00 |
Sub Total |
$1,482,339.00 |
NA |
$148,233.90 |
$100,155.42 |
$5,429.81 |
$8,152.86 |
$103,763.73 |
$118,587.12 |
Total |
$10,722,469.50 |
NA |
$5,884,666.95 |
$404,975.25 |
$20,001.10 |
$81,781.68 |
$180,050.34 |
$118,587.12 |
Table 3: Monthly Cash Flow
Production |
January |
February |
March |
April |
May |
June |
Onions |
$670,000.00 |
$670,000.00 |
$670,000.00 |
- |
- |
- |
Total Income |
$670,000.00 |
$670,000.00 |
$670,000.00 |
- |
- |
- |
Production |
July |
August |
September |
October |
November |
December |
Total |
Onions |
- |
- |
- |
$670,000.00 |
$670,000.00 |
$670,000.00 |
$4,020,000.00 |
Total Income |
- |
- |
- |
$670,000.00 |
$670,000.00 |
$670,000.00 |
$4,020,000.00 |
Operating Inputs |
January |
February |
March |
April |
May |
June |
Land Prep |
- |
- |
- |
- |
- |
- |
Fungicide/Bactericide |
- |
- |
- |
$21,300.00 |
$21,300.00 |
$21,300.00 |
Insecticide |
- |
- |
- |
$21,005.00 |
$21,005.00 |
$21,005.00 |
Herbicide |
- |
- |
- |
$10,765.00 |
$10,765.00 |
$10,765.00 |
Fertilizer |
- |
- |
- |
$20,000.00 |
$18,000.00 |
- |
Irrigation |
- |
- |
- |
$52,350.00 |
$52,350.00 |
$52,350.00 |
Hired Labor |
$66,666.67 |
$66,666.67 |
$66,666.67 |
$66,666.67 |
$66,666.67 |
$66,666.67 |
Harvesting |
- |
- |
- |
- |
- |
- |
Trucking |
- |
- |
- |
- |
- |
- |
Drying |
- |
- |
- |
- |
- |
- |
Ventilation |
- |
- |
- |
- |
- |
- |
Refrigeration |
$28,875.00 |
$28,875.00 |
- |
- |
- |
- |
Packing + Bags |
$115,500.00 |
$115,500.00 |
- |
- |
- |
- |
Operator Labor |
$2,500.00 |
$2,500.00 |
$2,500.00 |
$2,500.00 |
$2,500.00 |
$2,500.00 |
Accounting & Legal |
$166.67 |
$166.67 |
$166.67 |
$166.67 |
$166.67 |
$166.67 |
Fuel & Lube |
$6,241.43 |
$6,241.43 |
$12,482.85 |
$12,482.85 |
$12,482.85 |
$12,482.85 |
Maintenance |
$9,476.33 |
$9,476.33 |
$18,952.67 |
$18,952.67 |
$18,952.67 |
$18,952.67 |
Utilities |
$583.33 |
$583.33 |
$583.33 |
$583.33 |
$583.33 |
$583.33 |
Miscellaneous |
$166.67 |
$166.67 |
$166.67 |
$166.67 |
$166.67 |
$166.67 |
Interest OC |
$7,375.18 |
$7,375.18 |
$7,375.18 |
$7,375.18 |
$7,375.18 |
$7,375.18 |
Total Income |
$237,551.27 |
$237,551.27 |
$108,894.03 |
$234,314.03 |
$234,314.03 |
$214,314.03 |
Net Returns |
$432,448.73 |
$432,448.73 |
$561,105.97 |
$(234,314.03) |
$(234,314.03) |
$(214,314.03) |
Operating Inputs |
July |
August |
September |
October |
November |
December |
Total |
Land Prep |
- |
- |
$57,333.33 |
$57,333.33 |
$57,333.33 |
- |
$172,000.00 |
Fungicide/Bactericide |
$21,300.00 |
- |
- |
- |
- |
- |
$85,200.00 |
Insecticide |
$21,005.00 |
- |
- |
- |
- |
- |
$84,020.00 |
Herbicide |
$10,765.00 |
- |
- |
- |
- |
- |
$43,060.00 |
Fertilizer |
- |
- |
$263,600.00 |
- |
- |
- |
$301,600.00 |
Irrigation |
$52,350.00 |
- |
$34,900.00 |
$34,900.00 |
- |
- |
$279,200.00 |
Hired Labor |
$66,666.67 |
$66,666.67 |
$66,666.67 |
$66,666.67 |
$66,666.67 |
$66,666.67 |
$800,000.00 |
Harvesting |
- |
- |
$165,000.00 |
- |
- |
- |
$165,000.00 |
Trucking |
- |
- |
$82,500.00 |
$82,500.00 |
- |
- |
$165,000.00 |
Drying |
- |
- |
$99,000.00 |
- |
- |
- |
$99,000.00 |
Ventilation |
- |
- |
$1,980.00 |
$1,980.00 |
- |
- |
$3,960.00 |
Refrigeration |
- |
- |
$28,875.00 |
$28,875.00 |
$28,875.00 |
$28,875.00 |
$173,250.00 |
Packing + Bags |
- |
- |
- |
- |
- |
- |
$693,000.00 |
Operator Labor |
$2,500.00 |
$2,500.00 |
$2,500.00 |
$2,500.00 |
$2,500.00 |
$2,500.00 |
$30,000.00 |
Accounting & Legal |
$166.67 |
$166.67 |
$166.67 |
$166.67 |
$166.67 |
$166.67 |
$2,000.00 |
Fuel & Lube |
$12,482.85 |
$12,482.85 |
$12,482.85 |
$6,241.43 |
$6,241.43 |
$6,241.43 |
$118,587.12 |
Maintenance |
$18,952.67 |
$18,952.67 |
$18,952.67 |
$9,476.33 |
$9,476.33 |
$9,476.33 |
$180,050.34 |
Utilities |
$583.33 |
$583.33 |
$583.33 |
$583.33 |
$583.33 |
$583.33 |
$7,000.00 |
Miscellaneous |
$166.67 |
$166.67 |
$166.67 |
$166.67 |
$166.67 |
$166.67 |
$2,000.00 |
Interest OC |
$7,375.18 |
$7,375.18 |
$7,375.18 |
$7,375.18 |
$7,375.18 |
$7,375.18 |
$88,502.11 |
Total Income |
$214,314.03 |
$108,894.03 |
$784,749.03 |
$241,431.27 |
$122,051.27 |
$122,051.27 |
$3,492,429.57 |
Net Returns |
$(214,314.03) |
$(108,894.03) |
$(784,749.03) |
$428,568.73 |
$547,948.73 |
$547,948.73 |
$527,570.43 |