This publication presents sample costs and returns to produce vegetables using hoop house protection and drip irrigation in Southeastern Nevada. It is intended to be a guide, used to make production decisions, determine potential returns and prepare business and marketing plans. Practices described are based on the production practices considered typical for this crop and region, but may not apply to every situation. A “Your Farm” column in Table 1 is provided for your use. Funding for the research used to develop these results was provided by the National Institute of Food and Agriculture (NIFA).
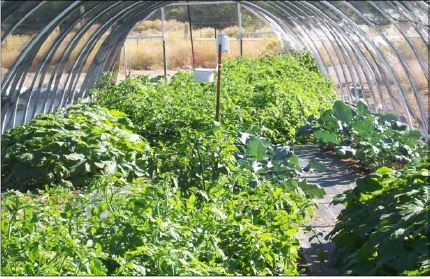
Assumptions
The following assumptions refer to Tables 1-3, and reflect the typical costs and returns to establish and produce vegetables using hoop house protection and drip irrigation in Southeastern Nevada. The practices described are not the recommendations of University of Nevada Cooperative Extension, but rather the production practices and materials considered typical of a wellmanaged hoop house operation in the region, as determined by the best available research. Costs, materials and practices are not applicable to all situations, as establishment and cultural practices vary among growers within the region.
Land
The hoop house is located on a portion of a 5 acre plot having either established agricultural water rights or a water lease. The remainder of the 5 acres is devoted to other crops. The hoop house is positioned near the producer’s home to facilitate daily visits. The 14-foot-by-90-foot hoop house (1,260 square feet) has 710 square feet of cultivated area for market crop production and 550 square feet used for row access. The land market value in 2010 was approximately $7,500 per acre for small land parcels with water rights.
Land Preparation
Prior to adding any amendments to the soil, the soil was tested to determine its nutrient content. One farm complete sample was analyzed at a cost of $47.50. Using custom hire services, the ground was plowed with a disc to break up the soil to improve water infiltration and fertilizer penetration at a cost of $50. Five inches of high quality compost that had been analyzed for nutrient quality and salt content were cultivated in at the same time for soil conditioning. The compost incurred a cost of $400, for complete land preparation costs of $497.50.
Hoop House Construction
The hoop house was constructed following the instructions in Utah State University Cooperative Extension publication HG/High Tunnels/2008-01, “Constructing a Low-cost High Tunnel” available at Low-cost High Tunnel.
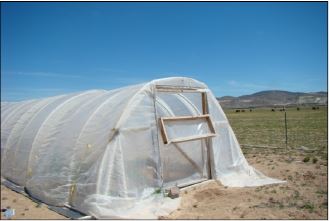
The hoop house was constructed with topventing wood frame doors at both ends for total material costs of $688.38. Transportation of materials incurred an additional cost of $60. Twenty-seven hours of owner/operator labor at a rate of $13 per hour and 19 hours of contract labor at a rate of $10 per hour were utilized to construct the hoop house for total labor costs of $541. The hoop house was built with support posts as suggested by USU for high wind or snow areas. The support posts were connected to the ridge purlin using recycled tire inner tubes, improving both strength and flexibility. The outside covering was secured against the end framing with wiggle wire, which is an upgrade from the USU model. Along the sides of the hoop house, the outside covering was anchored beside each rib with baling twine tied to each rebar anchor.
Black fabric ground cover at a cost of $209.15 was installed throughout the inside of the hoop house at the time of construction. Adding the ground cover was optional and was done for weed control. Planting areas were cut out to provide the spaces for the planting beds. Two planting beds measuring 89 feet x 2 feet and two planting beds measuring 88.5 feet x 2 feet were created, allowing for 356 and 354 square feet of planting space respectively, for a total of 710 square feet. Inside the hoop house, a 6 inch perimeter was left between planting beds and the inside walls to minimize frost damage to crops. Access pathways were 1.5 feet wide except for the middle path which were 2 feet wide. Total costs for the construction of the hoop house including labor and materials, except for the optional ground cover which is listed separately on the investment summary, were $1,289.38.
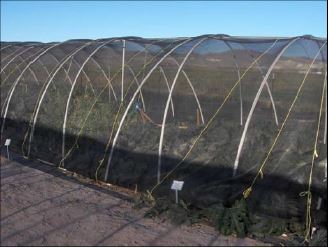
Planting Bed Layout inside the Hoop House
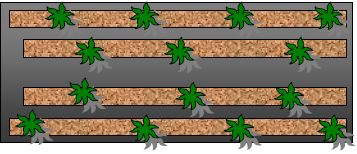
Production Cultural Practices and Material Inputs
Irrigation
For this publication, the hoop house was located 200 feet from the agricultural irrigation well. A ditcher was rented for one day at a cost of $100 to create a trench from the well to the hoop house for laying subsurface pipe to prevent freezing. A backup irrigation system is essential. This can be a large tank or a municipal water source. Installation of the pipe from the well and the drip system in the hoop house took approximately 40 hours of owner/operator labor at a rate of $13 per hour for a total labor cost of $520. The drip system consists of hoses, emitters and a timing device. Material costs for the drip system, filters and other necessary parts are $683.74 per hoop house. Total costs for installation of the irrigation system were $1,303.74. Irrigation through the drip system begins in April and ends the middle of October. Irrigation occurs daily, and sometimes twice a day for the summer crops. The winter crops are hand irrigated weekly or as needed. Access to a frost-free hydrant is necessary. The irrigation costs shown in Table 1 are calculated as a percentage of irrigation costs for the whole 5 acres including pumping costs and a portion of the water lease costs. Total irrigation costs excluding labor and the drip system are $16.20 per year for a hoop house.
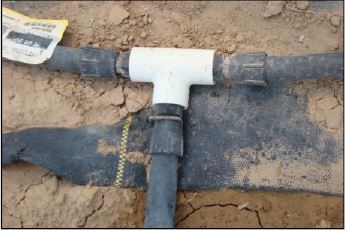
Crop Selection
The crops represented in this publication were chosen because of their profitability. A large selection of crops can be grown in the hoop house. Further information about all attempted crops for the hoop house will be available in the forthcoming publication, “Crops for Hoop House Production.” For this study, the objective was to utilize the hoop house to produce crops with the highest per-square-foot value. Any crops being considered for hoop house production should be those that cannot be obtained at the local grocery store, either because of variety, availability, quality or any combination thereof. To this end, crops were planted to meet the needs of high end urban chefs and local farmers markets. Tomato varieties were chosen for their qualities in flavor and texture. Golden zucchini were chosen for their uniqueness and the ability to harvest both fruit and blossoms, which are highly desirable by gourmet chefs. Baby greens, mustard, kale and spinach were selected for their cold hardiness and marketability.
Planting
Crops should be selected to achieve the broadest possible range of harvest dates by utilizing either different crops or different varieties of the same crop. Spring planting yields summer and fall harvests; fall planting yields late fall, winter or early spring harvests. Golden zucchini squash seed were planted on the two outside beds in early May. Tomato starter plants were planted on the two inside beds two weeks later. Trellises for support of the tomatoes consisted of t-posts and twine and were installed at the time of planting. Winter crops of baby greens, mustard, kale and spinach were planted in October. Plants may sprout but do not grow large enough for harvest until after Jan.1.
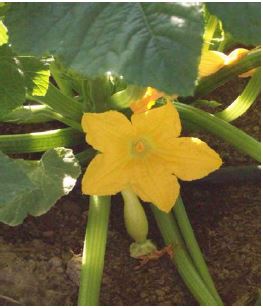
Fertilization
Liquid iron on demand fertilizers were spread by a hand-held sprayer when plants showed visible signs of deficiencies at a cost of $3. Fertigation (using a liquid-based fertilizer though an irrigation system) was dispensed by the drip irrigation system at a cost of $10 late in the season.

Seasonal Protection
Fifty percent shade cloth is used on the outside of the hoop house in the spring, summer and early fall at a cost of $315.28. Six mil plastic is used on the outside in the winter months, and is rolled up on the sides to allow for ventilation. The $225.00 cost for the plastic cover is included in the cost of the hoop house. Fabric row covers placed over the plants can be used as an extra layer of protection in the winter. The cost for the row covers was $73.45 with an additional cost of $39.99 for the pins to secure it.
Pest Management
The isolated desert environment typically decreases disease and insect infestations. Utilizing natural control methods reduces input costs. A variety of pest management methods were used depending on pest population cycles. Pest treatment will normally begin in April.
Weeds
Consumers prefer chemical free production. Therefore, weed control is by hand weeding constantly during the season and costs are included in labor calculations. The installation of the black fabric ground cover reduced the amount of labor needed for weed control and had the added benefit of keeping the produce cleaner.
Insects
Beneficial insects can thrive in the hoop house environment. Ladybugs were added as a preventative measure. Several insects are threats to vegetable production. Squash bugs were eliminated by hand vacuuming. Other pests include tomato caterpillars and leaf hoppers. Caterpillars and destructive worms were controlled by hand picking. In extreme cases organically approved insecticides were used for control. Total insect control costs were $0.05/sq ft not including labor.
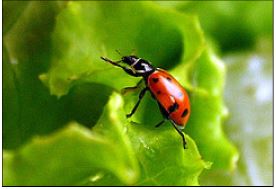
Vertebrates
Some gopher issues occurred within the hoop house. Mechanical traps can be utilized as controls.
Labor
The owner/operator cost of labor is based on an hourly wage of $13. The owner/operator is the sole employee for this enterprise except for contract labor to assist with construction and setup of the hoop house and irrigation system. During May and October, the owner/operator spent 38 and 32 hours respectively cleaning up from the previous harvest, preparing the soil and planting the new season’s crops. Most of June’s 18 hours were spent on maintenance. July through September is the most timeintensive period: between 54 and 72 hours a month. This accounts for increased harvest time and seven to nine hours per week to transport and market the produce to urban areas. November, December and January require minimal labor input for maintenance: two, four and nine hours respectively. In February, March and April 11 to 13 hours per month are split between maintenance and harvesting.
Harvest
Harvest of winter greens, including baby greens, mustard, spinach and kale, can commence and occur at varying times because their growth is dependent on winter sunny warm spells. They are harvested at a ‘baby’ size. Most winter greens can be harvested by February, and harvest can continue for five to seven pickings from the same planting. Zucchini is harvested when the fruits are approximately 5 to 6 inches long. Both male and female blossoms are harvested. Tomatoes are harvested when fully red.
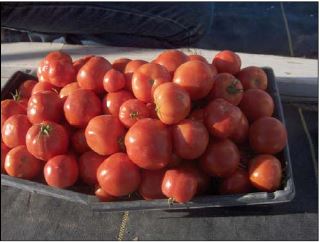
Yield
All yield numbers are adjusted for a 20 percent plant loss due to quality standards, disease, insects or other factors. Tomatoes yielded approximately 2.58 pounds per square foot. Golden zucchini yielded 4.5 pounds of fruit per square foot in addition to yields of one blossom per square foot per week for the 12-week harvest period. The yields per square foot were: 0.8 pounds for spinach, 0.6 pounds for mustard, 0.97 pounds for kale and baby greens had yields of 0.66 pounds per square foot.
Packaging
Tomatoes and the golden zucchini fruits are field packed into wax boxes at a cost of $1.00 per box. The zucchini blossoms and all winter greens are packed into clamshells at a cost of $0.16 per clamshell.
Marketing
Summer harvested crops are mostly sold to high-end urban chefs with the remainder being sold directly from a farm stand or at local farmers’ markets. Some late fall and early spring harvested baby greens could be transported to urban markets but most of the winter crops are sold locally.
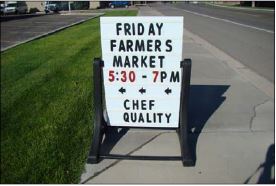
Transportation to Market
During the summer, produce is delivered to the urban market using a pickup truck pulling a cooler trailer. It is assumed in this publication that the hoop house is a two-hour drive from the urban market and that the cooler trailer is shared either with non-hoop-house crops from the same producer or with another producer. A cooler trailer is essential to maintain the superior quality required by highend buyers.
Returns
Returns are based on market prices received from farmers’ market sales and sales to chefs in urban areas. Returns can vary with EXTREME fluctuation both during the growing season and from year to year as well as differing by location due to market conditions. For this reason, risk analysis along with market analysis should be a consideration of any planting decisions. In this study, the combination of crops for the year had to produce $12.25 per sq. ft. of revenue to pay for the hoop house.
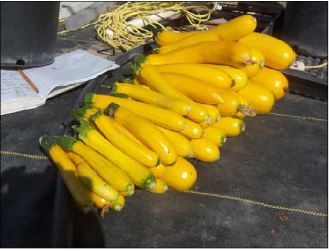
Overhead and Capital Recovery Costs
Cash Overhead
Cash overhead consists of various cash expenses paid during the year. These costs include property taxes, interest, office expenses, liability and property insurance and investment/machinery repairs. A complete listing of farm investments and associated costs can be found in Table 3.
Interest on Operating Capital
Total operating capital is calculated based on 80 percent of total operating (variable) costs. The interest on operating capital is calculated at a rate of 6.5 percent.
Property Taxes
Property taxes in Nevada differ across counties. For the purposes of this publication, investment property taxes are calculated at 1percent of the average asset value of the property.
Insurance
Insurance on farm investments vary, depending on the assets included and the amount of coverage. Property insurance provides coverage for property loss at a cost of 0.666 percent of the average asset value. Liability insurance covers accidents on the farm at an annual cost of $50.00.
Fuel and Lube
The fuel and lube for each piece of equipment is calculated at 8 percent of the average asset value.
Investment Repairs
Annual repairs on all farm investments or capital recovery items that require maintenance are calculated at 2 percent of the average asset value.
Office & Travel
Office and travel costs are estimated at $250 for an average year. These expenses include office supplies, telephone service, Internet service and travel expenses to educational seminars.
Pro-rated Expenses
Taxes, insurance, fuel and lube, maintenance, utilities, and office and travel expenses, have all been pro-rated to reflect the amount of time and land occupied by hoop house production.
Capital Recovery
Capital recovery costs are the annual depreciation (opportunity cost) of all farm investments. Capital recovery costs are calculated using straight line depreciation. Farm equipment may be purchased new or used, depending on producer preferences. The cost of land payments is not included in these calculations.
Salvage Value
Salvage value is 10 percent of the new purchase price, which is an estimate of the remaining value of an investment at the end of its useful life. The salvage value for land is the purchase price, as land does not normally depreciate.
Average Asset Value Computation
(Purchase Price + Salvage Value divided by 2)
Straight Line Depreciation Computation
(Purchase Price - Salvage Value divided by Useful Life)
Conclusions
Vegetable production in a hoop house can possibly pay your costs and a salary if higher return crops are selected. Each year the crops had to produce $12.25/sq. ft. in the 710 sq. ft. of production area to break even including reimbursement to the owner/operator of $13 per hour.
References
- Black, Brent, Dan Drost, Daniel Rowley & Rick Heflebower (2008). Constructing a Low-cost High Tunnel. Publication #HG/High Tunnels/2008-01pr. Utah State University Cooperative Extension.
- Cornell University (2010). Planning for Profit- How to Analyze High Tunnel Finances. How to Analyze High Tunnel Finances. Department of Horticulture, College of Agriculture and Life Sciences, Cornell University.
- Smathers, Robert (2007). The Costs of Owning and Operating Farm Machinery in the Pacific Northwest 2005. A Pacific Northwest Publication #346. University of Idaho, Washington State University, and Oregon State University.
Table 1: Southern Nevada Hoop House Production Costs and Returns, 2010. (710 sq ft. production area)
Gross Income |
Square feet |
Total Units |
Unit |
Price/Cost Per Unit |
Total Cost/Value |
Total Cost/Value Per Square Foot |
Your Farm |
Tomatoes |
354 |
913.32 |
lb |
$2.50 |
$2,283.30 |
$6.45 |
|
Golden Summer Squash |
356 |
1281.60 |
lb |
$2.00 |
$2,563.20 |
$7.20 |
|
Squash Blossoms |
356 |
4272.00 |
blossom |
$0.50 |
$2,136.00 |
$6.00 |
|
Baby Greens |
354 |
233.64 |
lb |
$3.50 |
$817.74 |
$2.31 |
|
Mustard |
89 |
53.40 |
lb |
$4.00 |
$213.60 |
$2.40 |
|
Kale |
89 |
86.33 |
lb |
$3.00 |
$258.99 |
$2.91 |
|
Spinach |
178 |
142.40 |
lb |
$3.00 |
$427.20 |
$2.40 |
|
Total Gross Income |
|
|
|
|
$8,700.03 |
$12.25 |
|
Operating Costs |
Total Units |
Unit |
Price/Cost Per Unit |
Total Cost/Value |
Total Cost/Value Per Square Foot |
Your Farm |
Seed |
8.00 |
Pkg |
$14.50 |
$116.00 |
$0.16 |
|
Starter Plants |
30.00 |
6 pack |
$1.50 |
$45.00 |
$0.06 |
|
Insecticide |
1.00 |
Quart |
$25.00 |
$25.00 |
$0.04 |
|
Fertilizer |
1.00 |
Quart |
$13.00 |
$13.00 |
$0.02 |
|
Irrigation |
1.00 |
Annual |
$16.20 |
$16.20 |
$0.02 |
|
Operator Labor |
320.00 |
Hourly |
$13.00 |
$4,160.00 |
$5.86 |
|
Accounting & Legal |
1.00 |
Annual |
$50.00 |
$50.00 |
$0.07 |
|
Fuel & Lube |
1.00 |
Annual |
$198.00 |
$198.00 |
$0.28 |
|
Maintenance |
1.00 |
Annual |
$127.61 |
$127.61 |
$0.18 |
|
Packaging |
2000.00 |
Clamshells |
0.16 |
$320.00 |
$0.45 |
|
Packaging |
300.00 |
Wax Boxes |
$1.00 |
$300.00 |
$0.42 |
|
Advertising/Signs |
2.00 |
Units |
$90.00 |
$180.00 |
$0.25 |
|
Transportation |
12.00 |
Trip |
$70.00 |
$840.00 |
$1.18 |
|
Miscellaneous |
710 |
Square Feet |
$0.20 |
$142.00 |
$0.20 |
|
Operating Capital Interest |
$4,983.85 |
$ |
$0.065 |
$161.98 |
$0.23 |
|
Total Operating Costs |
|
|
|
$6,694.78 |
$9.43 |
|
Income Above Operating Costs |
|
|
|
$2,005.25 |
$2.82 |
|
Ownership & Cash Overhead Costs |
Total Cost/Value |
Total Cost/Value Per Square Foot |
Your Farm |
Liability Insurance |
$50.00 |
$0.07 |
|
Office & Travel |
$250.00 |
$0.35 |
|
Annual Investment Insurance |
$46.78 |
$0.07 |
|
Annual Investment Taxes |
$81.97 |
$0.12 |
|
Total Cash Overhead Costs |
$428.75 |
$0.60 |
|
Noncash Overhead Costs (Capital Recovery) |
Total Cost/Value |
Total Cost/Value Per Square Foot |
Your Farm |
Buildings, Improvements, & Equipment |
$857.75 |
$4.29 |
|
Machinery & Vehicles |
$716.15 |
$3.58 |
|
Total Noncash Overhead Costs |
$1,573.90 |
$2.22 |
|
Total Ownership Costs |
$2,002.65 |
$2.82 |
|
Total Costs |
$8,697.43 |
$12.25 |
|
Net Projected Returns |
$2.60 |
$0.00 |
|
Table 2: Investment Summary for Hoop House Production
Buildings, Improvements, and Equipment |
Purchase Price |
% Use |
Purchase Price |
Useful Life (Yrs) |
Salvage Value |
Annual Capital Recovery |
Annual Insurance |
Annual Taxes |
Annual Repairs |
Land |
$37,500.00 |
7% |
$2,625.00 |
150.00 |
$2,625.00 |
- |
$17.48 |
$26.25 |
- |
Land preparation |
$497.50 |
100% |
$497.50 |
5.00 |
- |
$99.50 |
- |
- |
- |
Hoophouse |
$1,289.38 |
100% |
$1,289.38 |
5.00 |
- |
$257.88 |
- |
$6.45 |
$12.89 |
Ground Cover |
$209.15 |
100% |
$209.15 |
5.00 |
- |
$41.83 |
- |
- |
- |
Trellising |
$210.00 |
100% |
$210.00 |
10.00 |
$ 21.00 |
$18.90 |
- |
- |
- |
Row Cover and Pins |
$113.44 |
100% |
$113.44 |
5.00 |
- |
$22.69 |
- |
- |
- |
Shade Cloth |
$315.28 |
100% |
$315.28 |
5.00 |
- |
$63.06 |
- |
- |
- |
Implements |
$750.00 |
100% |
$750.00 |
10.00 |
$75.00 |
$67.50 |
- |
|
$8.25 |
Drip Irrigation System |
$1,303.74 |
100% |
$1,303.74 |
5.00 |
- |
$260.75 |
- |
- |
$13.04 |
Water Tank |
$285.00 |
100% |
$285.00 |
10.00 |
$28.50 |
$25.65 |
- |
- |
$3.14 |
Sub Total |
$42,473.49 |
|
$7,598.49 |
|
$2,749.50 |
$857.75 |
$17.48 |
$36.82 |
$37.32 |
Buildings, Improvements, and Equipment |
Purchase Price |
% Use |
Purchase Price |
Useful Life (Yrs) |
Salvage Value |
Annual Capital Recovery |
Annual Insurance |
Annual Taxes |
Annual Repairs |
Annual Fuel & Lube |
Cooler Trailer |
$6,996.70 |
50% |
$3,498.35 |
15.00 |
$349.84 |
$209.90 |
$12.81 |
$19.24 |
$38.48 |
- |
1/2 Ton Pickup |
$30,000.00 |
15% |
$4,500.00 |
8.00 |
$450.00 |
$506.25 |
$16.48 |
$24.75 |
$49.50 |
$198.00 |
Sub Total |
$36,996.70 |
|
$7,998.35 |
NA |
$799.84 |
$716.15 |
$29.30 |
$43.99 |
$87.98 |
$198.00 |
Total |
$79,470.19 |
|
$15,596.84 |
|
$3,549.34 |
$1,573.90 |
$46.78 |
$80.81 |
$125.30 |
$198.00 |
Table 3: Monthly Cash Flow
Production |
January |
February |
March |
April |
May |
June |
Tomatoes |
- |
- |
- |
- |
- |
- |
Golden Summer Squash |
- |
- |
- |
- |
- |
$128.16 |
Squash Blossoms |
- |
- |
- |
- |
- |
$106.80 |
Baby Greens |
- |
$245.32 |
$ 327.10 |
$327.10 |
$81.77 |
- |
Mustard |
- |
$71.20 |
$ 7 1.20 |
$71.20 |
- |
- |
Kale |
- |
$32.37 |
$ 6 4.75 |
$97.12 |
$64.75 |
- |
Spinach |
- |
$53.40 |
$ 106.80 |
$160.20 |
$106.80 |
- |
Total Income |
- |
$402.30 |
$569.84 |
$655.62 |
$253.32 |
$234.96 |
Production |
July |
August |
September |
October |
November |
December |
Total |
Tomatoes |
$456.66 |
$913.32 |
$913.32 |
- |
- |
- |
$2,283.30 |
Golden Summer Squash |
$897.12 |
$897.12 |
$640.80 |
- |
- |
- |
$2,563.20 |
Squash Blossoms |
$747.60 |
$747.60 |
$534.00 |
- |
- |
- |
$2,136.00 |
Baby Greens |
- |
- |
- |
- |
- |
- |
$817.74 |
Mustard |
- |
- |
- |
- |
- |
- |
$213.60 |
Kale |
- |
- |
- |
- |
- |
- |
$258.99 |
Spinach |
- |
- |
- |
- |
- |
- |
$427.20 |
Total Income |
$2,101.38 |
$2,558.04 |
$2,088.12 |
- |
- |
- |
$8,700.03 |
Operating Inputs |
January |
February |
March |
April |
May |
June |
Seed |
- |
- |
- |
- |
- |
- |
Starter Plants |
- |
- |
- |
- |
$45.00 |
- |
Insecticide |
- |
- |
- |
$2 5.00 |
- |
- |
Fertilizer |
- |
- |
- |
- |
$13.00 |
- |
Irrigation |
- |
- |
- |
$6 .08 |
$2.03 |
$2 .03 |
Operator Labor |
$117.00 |
$143.00 |
$143.00 |
$169.00 |
$494.00 |
$234.00 |
Accounting & Legal |
$4 .17 |
$4.17 |
$4.17 |
$4.17 |
$4.17 |
$4.17 |
Fuel & Lube |
$10.42 |
$10.42 |
$20.84 |
$20.84 |
$20.84 |
$20.84 |
Maintenance |
$6 .72 |
$6.72 |
$13.43 |
$ 13.43 |
$13.43 |
$13.43 |
Packaging |
- |
- |
- |
- |
- |
- |
Packaging |
- |
- |
- |
- |
- |
- |
Advertising |
- |
- |
- |
- |
- |
$ 9 0.00 |
Transportation to Market |
- |
- |
- |
- |
- |
- |
Miscellaneous |
$11.83 |
$11.83 |
$11.83 |
$11.83 |
$11.83 |
$11.83 |
Interest OC |
$13.50 |
$13.50 |
$13.50 |
$13.50 |
$13.50 |
$13.50 |
Total Operating Costs |
$1 63.64 |
$1 89.64 |
$206.77 |
$263.85 |
$617.80 |
$389.80 |
Net Returns |
$(163.64) |
$212.66 |
$363.07 |
$391.77 |
$ (364.48) |
$(154.84) |
Operating Inputs |
July |
August |
September |
October |
November |
December |
Total |
Seed |
- |
- |
- |
- |
$116.00 |
- |
$116.00 |
Starter Plants |
- |
- |
- |
- |
- |
- |
$45.00 |
Insecticide |
- |
- |
- |
- |
- |
- |
$25.00 |
Fertilizer |
- |
- |
- |
- |
- |
- |
$13.00 |
Irrigation |
$2.03 |
$2.03 |
$2.03 |
- |
- |
- |
$16.20 |
Operator Labor |
$702.00 |
$936.00 |
$728.00 |
$416.00 |
$26.00 |
$52.00 |
$4,160.00 |
Accounting & Legal |
$4.17 |
$4.17 |
$4.17 |
$4.17 |
$4.17 |
$4.17 |
$50.00 |
Fuel & Lube |
$20.84 |
$20.84 |
$20.84 |
$10.42 |
$10.42 |
$10.42 |
$198.00 |
Maintenance |
$13.43 |
$13.43 |
$13.43 |
$6.72 |
$6.72 |
$6.72 |
$127.61 |
Packaging |
- |
- |
- |
- |
- |
$320.00 |
$320.00 |
Packaging |
- |
- |
- |
- |
- |
$300.00 |
$300.00 |
Advertising |
- |
$90.00 |
- |
- |
- |
- |
$180.00 |
Transportation to Market |
$168.00 |
$336.00 |
$336.00 |
- |
- |
- |
$840.00 |
Miscellaneous |
$11.83 |
$11.83 |
$11.83 |
$11.83 |
$11.83 |
$11.83 |
$142.00 |
Interest OC |
$13.50 |
$13.50 |
$13.50 |
$13.50 |
$13.50 |
$13.50 |
$161.98 |
Total Operating Costs |
$935.80 |
$1,427.80 |
$1,129.80 |
$462.64 |
$188.64 |
$718.64 |
$6 ,694.78 |
Net Returns |
$1,165.58 |
$1,130.24 |
$958.32 |
$(462.64) |
$(188.64) |
$(718.64) |
$2 ,005.25 |