INTRODUCTION
Farm owners/managers must answer several economic questions annually to determine the business feasibility of their operation. These questions may include: Which crops to produce? How many acres of each crop to produce? What size product or retail cut to sell? Will projected income for the coming year be sufficient to cover expenses and family living requirements? Answering these questions, followed by appropriate management, will determine the farm's production and economic performance.
The budgeting process provides a basic source of information for making farm management decisions. Budgeting is concerned with the coordination of resources, production, and expenditures. This process is often referred to as farming on paper, or a financial road map for the next production period to be incorporated in the farm business plan. Budgets are constructed to estimate the outcomes of activities in the future, as opposed to records, which are summaries of past outcomes. Budgeting allows for estimates to be made on paper, prior to the commitment of funds or resources to an activity, allowing for the anticipation and avoidance of problems that will likely be encountered based on historical records.
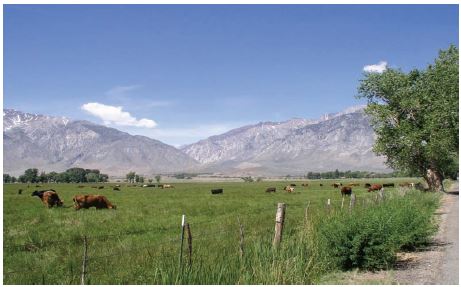
TYPES OF FARM/RANCH BUDGETS
There are four general types of farm/ranch budgets: whole-farm, partial, cash flow, and enterprise. A whole-farm budget is normally constructed on an annual basis and includes all the income and costs associated with a farm’s yearly production. It summarizes the major physical and financial features of the entire farm. Some of the major uses of whole-farm budgets are: 1) To compare alternative farm organizations under different cropping or production patterns, 2) to estimate the profitability of a given farm plan, and 3) to provide lenders, consultants, and others with a detailed farm plan for the coming year.
A partial budget examines relatively minor changes in a whole farm plan and includes only increases or decreases in expected revenues and expenses. For example, the partial budget approach may be used to determine whether custom hiring or owning harvest equipment would be most economically efficient. Partial budgeting analysis might also be used to determine the economics of raising and harvesting hay versus buying hay on the market. Since a partial budget examines only changes in farm plans, it is much quicker to construct than a whole farm budget.
A cash flow budget is concerned with the timing of receipts and expenses for a production period. Cash flow budgets are usually constructed on a monthly basis. They provide the owner/manager and lenders with information useful in estimating the amount and timing of borrowing and repayment of operating credit. Most lenders require a cash flow budget before extending credit.
Enterprise budgets form the basis for constructing whole farm, partial, and cash flow budgets. An enterprise budget includes all the costs and returns associated with producing one enterprise in a particular manner. Enterprise budgets are constructed on a per unit basis, such as per acre or per head, to facilitate comparisons among alternative enterprises. An enterprise is any activity which results in a product used on the farm or sold in the market. Examples of enterprises include an acre of wheat, a cow producing calves, and an acre of summer fallow ground. A farm is made up of one or more enterprises, each requiring a certain combination of resources.
Enterprise budgets are useful for estimating costs and returns on enterprises currently in the farm plan, as well as new enterprises under consideration. Most enterprise budgets also list physical resources needed for production, which is useful information for prospective new producers. In addition to producers, other agribusiness professionals often find enterprise budgets to be valuable information sources. These include lenders, assessors, appraisers, consultants, and lawyers.
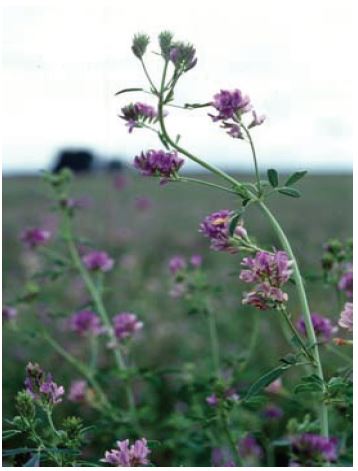
An enterprise budget represents the expected costs and returns associated with a particular farm situation. A hay enterprise budget might be constructed based on 125 acres of alfalfa in a certain area using 100 pounds of sulfur per acre. This enterprise budget will be very different than one representing 1,200 acres of alfalfa in a different area using only 50 pounds of sulfur per acre. This means that an enterprise budget constructed for one area may not be entirely appropriate for another area, yet it could be used for the baseline data or for comparison purposes.
Enterprise budgets can be detailed and time-consuming to construct. Also, data for enterprise budgets are often difficult to find, especially if creating a budget for an enterprise that has never been produced in a given area. To provide assistance to producers, Cooperative Extension across the West publishes representative budgets for various regions and commodities. It is important to stress that these budgets are not averages, but represent typical parameters to a common area. This distinction will become clear as a description of how enterprise budgets are constructed is revealed.
ENTERPRISE BUDGET CONSTRUCTION
The procedures and assumptions used in constructing an enterprise budget affect the way in which it should be interpreted. Cooperative Extension attempts to create budgets in a similar manner, stating major assumptions used in budget construction. Keep in mind that the budgets are meant to be representative of a typical situation, but do not exactly reflect a given operation.
For budgeting purposes, most states are divided into regions or production areas. The regions are grouped by production practices and/or land areas to reflect similar soil, weather, and economic conditions. Budgets are constructed for most of the major crop and livestock enterprises found in each region. Cultural operations and practices are assumed to be similar within each region, unless otherwise noted on individual budgets.
The first step in constructing a published enterprise budget is to identify the enterprise and region. Next, a group of Cooperative Extension agents and specialists meet with producers and lenders from the region who are familiar with the enterprise. During the meeting, cultural practices, and operations are discussed for the entire production cycle. All of the resources necessary for production are identified, along with their rates of use and cost.
The production cost and return data are entered in a computer program that organizes the data, calculates results, and prints out the budgets in a standard format. A draft budget is reviewed by producers and Cooperative Extension staff and revised. The final budget is published along with two or three pages of supporting text and tables.
The budget formats used vary according to type of enterprise. Crop budgets are itemized by operation, while livestock budgets are itemized by resource. If the crop is a perennial, the publication will contain an establishment budget, as well as an annual production budget.
ENTERPRISE BUDGET COMPONENTS
Every enterprise budget has three main parts: income, variable costs, and fixed costs. Other features of enterprise budgets are discussed under separate subheadings. Table 1 provides an example of a typical grass hay enterprise budget.
Income
Income is identified in the first section of the budget. Income shows the product(s) produced, the quantity and unit of each product, and the expected price per unit. Total income (revenue) per product is simply the quantity multiplied by the per unit price. For example, 1.5 tons per acre at $60 per ton is $90 in revenue per acre. Note that most budgets include a blank for users to enter expected income. Income is easy to calculate, but it requires careful consideration of expected yields and prices. Some budgets reflect yields and prices that are thought to be representative in three out of five years. This points out once again that the budgets must be customized for a particular market and output levels. The purpose of the enterprise budget may affect the yield and price estimates. If the ultimate objective is to project the next year’s cash flow budget, more specific information about market surpluses or deficits might provide estimates that differ considerably from long-term averages. If the objective is to construct a long-term, whole-farm planning budget, estimates more in line with long-term farm averages should be used.
Variable (Operating) Costs
Variable costs are the second set of values in the budget. Variable costs are those cost that vary with changes in production. Variable costs are grouped according to stage of production. Within each stage of production, operations are listed in the order they are performed such as harrowing, disking, plowing, seeding, etc. There are two types of variable costs: cash and noncash. Cash costs are incurred for items such as fuel, baling twine, and repairs. Noncash costs are incurred for labor supplied by the farm operator. Unless otherwise stated, most budgets treat labor as if it is operator labor and, therefore, noncash cost.
For each cultural operation, costs are included for labor, machinery, and materials. Quantities and prices are included for any materials used. For example, in the bale hay operation of a budget, the variable costs include a per acre labor charge, machinery cost, and materials cost. The labor charge is based on the time required per acre to bale the hay, allowing time for setting up, adjusting, and putting away oil lubricants, and repairs for the tractor and baler. The materials cost is for twine, based on the number of boxes of twine at a given price per acre. Then the total variable cost of baling the hay is listed per acre.
Operating capital interest is charged on all variable cash expenses to reflect the opportunity cost of short-term capital invested in the production of this crop. An opportunity cost is the return that could be realized if the funds for these expenses were invested in another alternative—a savings account for example. Interest is charged from the dates the expenses are incurred until the date the product is sold at an interest rate that is stated in the supporting text accompanying the budget. Operating capital interest is $.82 per acre in the grass hay budget (Table 1).
When the variable cost for each grass hay production stage is totaled (pre-harvest, harvest, and operating capital interest charges) total per-acre variable costs are $24.44. Total gross income minus total variable cost is $65.75 per acre. We can see from this budget, that in the short-run, income more than covers variable costs. Whatever income remains will be used to pay for the fixed factors of production.
Fixed (Ownership) Costs
The fixed costs of production are shown in the next section of the budget. They represent costs that are incurred, whether production of the enterprise occurs or not, once the land, machinery, and equipment necessary for the enterprise have been obtained. Fixed costs are often referred to as ownership costs or sunk costs. It should be emphasized that if the enterprise budget is for a new enterprise, and the necessary land, machinery and equipment have not yet been obtained, these ownership costs are still avoidable at that point by not producing and not obtaining the assets. Like variable costs, fixed costs are also divided into cash and noncash costs. Cash costs include cash leases, insurance, and taxes on machinery, equipment, buildings, and land. Cash fixed costs in Table 1 are estimated to be $7.36 per acre.
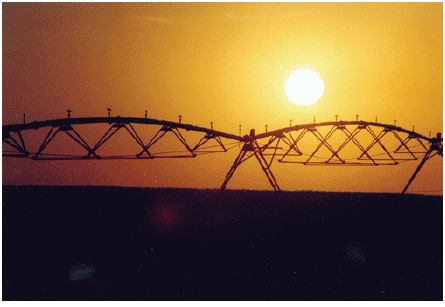
Noncash fixed costs consist of interest and depreciation, where all interest is treated as an opportunity cost. In some cases, machinery and equipment are partially debt financed. The interest on the loan is treated as a cash fixed cost, and the opportunity cost on the equity portion is a noncash fixed cost. Depreciation of machinery and equipment must be included in enterprise budgets, to reflect the fact that in the long-run a crop must pay for replacement of machinery and equipment used in its production. Depreciation provides a means of spreading replacement costs over the useful lives of machinery and equipment. Since land does not wear out (if properly maintained), there is no depreciation charge.
Interest costs are included as opportunity costs to reflect the fact that capital invested in farmland, machinery, breeding livestock, and buildings could be invested in other interest-earning assets. The interest rate used represents real rates of interest and are calculated by subtracting inflation rates from long-term interest rates. Total noncash fixed costs are estimated to be $44.68 per acre in the grass hay budget (Table 1).
Fixed costs of production per acre tend to vary greatly from one farm to another, and the fixed costs included in budgets should be viewed as a guide to constructing actual costs. If land is rented, include the cost of the lease as a cash fixed cost and eliminate the land interest charge and property taxes. If all machinery work is custom hired, eliminate all fixed machinery costs and include all the custom charges under the appropriate variable machinery cost headings. If land is owned and has outstanding debts against it, include mortgage interest payment as cash fixed costs and charge a noncash land interest cost against the equity. If the value of land reflects significant non-agricultural or speculative demand (if, for example, it is located near an urban area) it probably isn’t very realistic to expect an agricultural enterprise to be able to cover the full opportunity cost. It may be more realistic to charge the enterprise the net rental price, i.e., the expected rent payment for similar agricultural land. These examples illustrate the diversity of situations that exist with respect to fixed costs. Enterprise budgets must be modified to fit the actual production situation.
The grass hay budget in Table 1 estimates total fixed costs at $52.04 per acre by adding cash fixed costs and noncash fixed costs. The total cost of production is $76.29 per acre, which includes total variable costs plus total fixed costs. By subtracting total costs from total gross income, a profit of $13.71 is calculated for net projected returns. Thus, the budget estimates that over a long time period, the grass hay crop is paying for all the resources used in its production. This will be discussed further in the interpretation section.
Establishment Costs
In budgets for perennial crops with establishment year(s), an important fixed cost in the full production year budget would be an amortized establishment cost. Table 2 provides a budget focusing on a crop with an establishment year. This example budget evaluates the establishment and production budgets for a hay operation. In the first year, the net projected returns, after crediting for the harvest of an oat hay nurse crop, is a loss or cost of $60.26. This cost is carried into year two with an additional 6 percent interest charge to reflect the opportunity cost of investing the money in hay establishment. The total establishment cost is the net projected return at the end of year two, a net loss of $220.06.
The total establishment cost of $220.06 can be regarded as if it were a loan that needs to be paid off, with interest, in the eight full production years (six to eight years is common). Using a standard financial table like those used by lenders for loan amortization, the factor for an eight-year loan at 6 percent interest is 0.161. This gives an amortized or annual cost of $35.42. Again, once the crop is established, this is a fixed or sunk cost that cannot be avoided by discontinuing hay production.
Break-even Analysis
Break-even analysis can be conducted utilizing enterprise budgets. The goal of calculating a break-even price is to find out at what price a product would have to be sold for in the market place in order to pay for its production. In economics, break-even analysis can be performed at various levels. A break-even may be calculated to cover the total variable cost or the total cost.
When evaluating a business and its survivability in the short-run, some will look at only variable costs. That is, if a business can cover its variable costs (some refer to variable costs, as out of pocket costs) it will survive for a few years by selling its product at this level. This break-even can be calculated by dividing total variable cost by the expected yield. In Table 1, a break-even price of $16.17 per ton over variable cost is estimated. This price represents the minimum price at which hay could be sold to cover total variable cost to stay in business this production period.
However, for an operation to remain in business in the long-run, a break-even price that covers all costs is required. Products must be sold at a price level high enough to cover total production costs in order to ensure profit and business sustainability. In Table 1 the break-even price over total cost of $50.86 per ton (calculated by dividing total cost by yield) represents the minimum price at which hay could be sold to cover all costs of production. A price received greater than the break-even price would result in a profit. In the long-run, the break-even price over total cost should be equal to or less than average market prices.
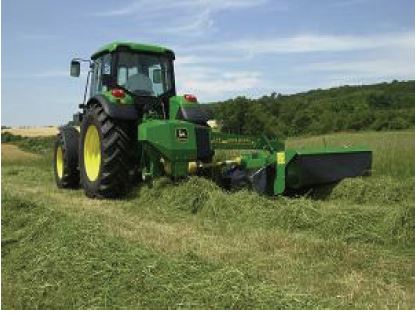
Machinery Costs
Machinery costs, both variable and fixed, often represent a substantial portion of the costs included in enterprise budgets. For that reason, detailed tables showing the values and associated costs of machinery and equipment are included with budgets. The machinery tables associated with this hay budget are shown in Tables 3 and 7.
Table 3 displays all the machinery and equipment used in the budget along with the major assumptions regarding their values and use. The list price represents the purchase value for each item. Although this may overstate current production costs, it does provide an indication of the enterprise’s ability to generate earnings to replace depreciable assets. This ability is critical if examining an enterprise’s long-run viability. The salvage value is an estimate of the assets’ value at the end of its useful life. Salvage values typically range from 10 to 30 percent of list prices. The current market value is calculated by adding the list price to the salvage value and dividing the total by 2. The result is the average value of the asset, and this implies that one half of its useful life remains. Producers and engineers estimate useful life. Remaining life is one-half of useful life, again reflecting that the assets have half of their life remaining. Hours of annual use are calculated based on the size, speed, and efficiency of each asset and its use in this and other enterprises.
The costs of owning and operating the machinery are shown in Table 4. These costs are calculated from equations based on economic and engineering relationships` and provide ballpark figures. The only way of accurately estimating machinery costs is by keeping detailed machinery use time logs, repair, and maintenance logs, fuel usage charts, and ownership records.
Machinery costs are divided into variable and fixed costs. Variable machinery costs include fuel, oil, lubricants, repairs, and maintenance charges. These costs are calculated based on current values, annual use, size, and horsepower ratings. Machinery total variable costs per hour are multiplied by hours of use per acre to obtain variable costs per acre.
Machinery fixed costs include depreciation, interest, and insurance. Cost per hour for each of these is based on asset values, ages, annual use, and interest rates. Fixed costs per hour are multiplied by asset use per acre to calculate fixed costs per acre. Total fixed costs per acre in Table 4 correspond to the fixed machinery costs included in the budgets. For example, total fixed costs per acre in Table 4 of $25.04 correspond to machinery and equipment insurance of $1.36 plus machinery and equipment interest and depreciation of $23.68, as shown in Table 1.
Annual use in Table 3 should include the use by all enterprises on the farm, not just the enterprise included in this particular budget. Since whole farm fixed costs tend not to change with amount of use, fixed cost per acre is overestimated if total fixed costs are divided by the number of acres for a single enterprise.
Total machinery cost per acre is estimated by adding variable plus fixed machinery cost per acre. In Table 4, estimated total machinery cost per acre is $33.82. This shows that machinery costs account for approximately 44 percent of the total cost per acre of grass hay production, highlighting the importance of machinery cost estimation in enterprise budgets.
LIVESTOCK ENTERPRISE DIFFERNECES
Livestock budgets are quite similar to crop budgets, but there are some differences in the production process which are discussed in this section. The example shown in Table 5 is a cow-calf enterprise budget. In many livestock enterprises there are several different products sold, such as different classes of livestock and in some enterprises, livestock products such as milk, eggs, or wool. This makes the estimation of expected yields and prices somewhat more complicated than for crop enterprises, where there is typically only one class of product sold.
The second difference is that returns and costs are estimated both on a herd or total enterprise basis and on a per unit basis as well. It is easier to estimate many of the costs and returns on a whole enterprise basis and then calculate it per unit by simple division. The third difference, previously noted is that cash variable costs are arranged by resource rather than by operation. As many livestock production activities tend to be applied to the whole herd at once, they don’t tend to break down neatly into discrete production operations. A final difference is the lack of break-even analysis on the product price. Since there are typically several different sales categories (six in this example), it is impossible to calculate a single break-even price.
INTERPRETATION
Three important points should be considered when interpreting enterprise budgets:
1. Enterprise budgets represent a point on a production function.
Enterprise budgets do not represent the only way or necessarily the best way to produce a crop—they represent one way. The production practices and inputs included in a budget reflect what is typically done in the area, but that does not imply that it is the profit maximizing method of production. Changes in fertilization, spraying, and field operations can drastically affect yields and costs. An enterprise budget shows one production regime and the yield associated with it. Many other combinations of inputs and outputs exist, making up the enterprise’s production function. An enterprise budget is simply one point on this function. The enterprise budget is a good source of economic information, but does not take the place of guides, soil analyses, and consultant recommendations.
2. Enterprise budgets are not precise.
Enterprise budgets appear to be very accurate. Dollar values are carried to two decimal places, and they appear to be exact and precise. In reality, every number in a budget should be treated as an estimate. Dollar values are printed to two decimal places because that is the way computer programs calculate them, avoiding rounding problems that might occur otherwise. None of the budgets will accurately represent any particular farm, and hence, should be used only as a guide.
3. Enterprise budgets stress economic costs and returns.
Enterprise budgets include both cash and noncash expenses for all resources used in production, except management. Remember the budget provided for the operator’s labor, but not for his or her responsibility for making decisions and bearing risk. This means that the budgets report economic costs and returns. What does the bottom line, the net projected return, actually mean to the farm operator or manager? A loss or negative figure doesn’t necessarily imply that the enterprise is a losing proposition and should be discontinued. For example, the calculated total cost per acre in the hay budget (Table 1) is $76.29. This includes noncash costs of $9.97 for labor and $44.68 for noncash fixed costs. Subtracting these from total costs leaves a total cash cost of $21.64. If the hay is sold for $60.00 per ton, then net cash returns are $90.00 minus $21.64, or $68.36 per acre. In any typical year, expected net cash returns would be over $60.00 per acre. However, in the long-run, other costs must be covered. Machinery and equipment must be rebuilt or replaced as it wears out, perennial crops need to be reestablished periodically, and the operator’s labor must be paid. With the inclusion of noncash costs, the generated budget is reflective of the long-term total cost of the enterprise. In evaluating the bottom line, an operator needs to decide whether the return to management that the net projected return implies is enough to justify the risks born in producing that particular crop. Another consideration is the alternative use for the land and labor. If there are no better alternatives, you would continue to produce native grass hay even if it shows a loss to management. For cash flow planning, cash costs and returns are used for enterprise selection.
SUMMARY
Of the four types of budgets, whole-farm, partial, enterprise, and cash flow, the enterprise budget provides the best means to evaluate the potential profitability for a given enterprise or farm income source. Developing an enterprise budgets allows for the identification of costs, both variable and fixed, and returns associated with the production and marketing of a product.
By understanding the basic concepts and formats of an enterprise budget, a user will be better able to analyze short and long-run fiscal impacts and evaluate profitability, as changes in break-even prices occur due to input cost and market pressures. Utilizing enterprise budgets developed by the University of Nevada Cooperative Extension provides producers an example format for evaluating current and potential profit centers in their agricultural operation.
Enterprise budgets for primary agricultural products in the State of Nevada can be found on the Extension website.
REFERENCES
Business Management in Agriculture (1987). Oregon State University Extension Publication EM 8339, September 1987.
Darden, T., Riggs, W., Torell, R., and Myer, G. (2000). Cow-Calf Costs and Returns for Elko County, Nevada Northeastern Nevada Production Area, 600 Cow Operation. Extension, Fact Sheet FS-01-19.
Doye, D and Sahs, R. (2005). Using Enterprise Budgets in Farm Financial Planning. Extension.
Hinman, Herbert (2002). Understanding and Using WSU Enterprise Budgets. Washington State University Cooperative Extension.
Table 1. Native grass hay production costs and returns (per acre)
Gross Income |
Quantity |
Unit |
S/Unit |
Total |
Your Costs |
Native Grass Hay |
1.50 |
Ton |
60.00 |
$90.00 |
|
Total Gross Income |
|
|
|
$90.00 |
|
Operating Costs (Preharvest & Harvest) |
Labor |
Machinery |
Materials |
Total |
Your Costs |
Ditch Maintenance (PreHarvest) |
0.56 |
0.00 |
0.50 |
$1.06 |
|
Misc. Materials 1.00Ac x 0.5 Spring Harrowing (PreHarvest) |
0.86 |
0.57 |
0.00 |
$1.43 |
|
Cut Hay (Harvest) |
1.93 |
2.71 |
0.00 |
$4.64 |
|
Rake Hay (Harvest) |
1.28 |
1.01 |
0.00 |
$2.30 |
|
Bale Hay (Harvest) |
1.93 |
2.87 |
2.90 |
$7.69 |
|
Bailing Twine 0.17 Box x 16.80 Accumulate Bales (Harvest) |
1.10 |
0.77 |
0.00 |
$1.87 |
|
Haul Hay (Harvest) |
2.31 |
2.33 |
0.00 |
$4.44 |
|
Total Preharvest Costs |
1.42 |
0.57 |
0.50 |
$2.49 |
|
Total Harvest Costs |
8.55 |
9.69 |
2.90 |
$20.94 |
|
Operating Capital Interest |
|
|
|
$0.82 |
|
Total Operating Costs |
|
|
|
$24.25 |
|
Ownership Costs (Cash & Noncash Costs) |
Unit |
Total |
Your Costs |
Machinery & Equipment Insurance (Cash) |
Acre |
$1.36 |
|
Property Taxes (Cash) |
Acre |
$6.00 |
|
Machinery & Equipment - Interest & Depreciation (Noncash) |
Acre |
$23.68 |
|
Land Interest Charge ($350 @ 6%) (Noncash) |
Acre |
$21.00 |
|
Total Cash Costs |
|
$7.36 |
|
Total Noncash Costs |
|
$44.68 |
|
Total Ownership Costs |
|
$52.04 |
|
Total Costs |
|
$76.29 |
|
Net Projected Returns |
|
$13.71 |
|
Break-Even Price, Total Operating Costs |
Ton |
$16.17 |
|
Break-Even Price, Total Costs |
Ton |
$50.86 |
|
Table 2. Hay establishment production costs and returns (per acre)
Year 1 Gross Income |
Unit |
Total |
Oat Hay |
3 tons at $60.00 per ton |
$180.00 |
Total Costs |
|
$240.26 |
Net Projected Returns |
|
$60.26 |
Year 2 Gross Income |
Unit |
Total |
Oat & Alfalfa Hay |
2.5 tons at $65.00 per ton |
$162.50 |
Year 1 Costs |
$60.26 at %6 opportunity costs |
$63.88 |
Other Costs (fixed/Variable) |
|
$318.68 |
Net Projected Returns |
|
$220.06 |
Year 3 Gross Income |
Unit |
Total |
Alfalfa Hay |
4.0 tons at $65.00 per ton |
$260.00 |
Amortized Establishment Costs |
$220 x .161 |
$35.42 |
Other Costs (fixed/Variable) |
|
$370.53 |
Net Projected Returns |
|
$145.95 |
Table 3. Machinery cost and usage assumptions
Machine |
Size |
List Price |
Current Market Value |
Salvage Value |
Useful Life |
Remaining Life |
Annual Use |
Loader Tractor |
50 hp |
$13,500 |
$8,775 |
$4,050 |
10,000 hr |
5,000 hr |
170.00 hr |
Loader Tractor |
75 hp |
$15,500 |
$10,075 |
$4,650 |
10,000 hr |
5,000 hr |
220.00 hr |
Swather |
12 ft |
$26,000 |
$18,200 |
$10,400 |
1,500 hr |
750 hr |
100.00 hr |
Bale Accumulator |
|
$2,500 |
$1,250 |
$0 |
600 hr |
300 hr |
60.00 hr |
Baler |
|
$18,000 |
$9,900 |
$1,800 |
1,000 hr |
500 hr |
100.00 hr |
Farmhand Loader |
|
$3,200 |
$1,840 |
$480 |
2,400 hr |
1,200 hr |
120.00 hr |
Harrow |
10 ft |
$1,000 |
$500 |
$0 |
450 hr |
225 hr |
45.00 hr |
Hay Wagon |
|
$3,500 |
$2,013 |
$526 |
2,400 hr |
1,200 hr |
120.00 hr |
Side Delivery Rake |
10 ft |
$4,000 |
$2,200 |
$400 |
700 hr |
350 hr |
70.00 hr |
Table 4. Machinery cost calculations (Cost per Hour & Acre)
Machine |
Size |
Fuel & Lube |
Repair & Maint. |
Depr. & Interest |
Insurance |
Total Cost |
Hours Per Acre |
Variable |
Fixed |
Total |
Loader Tractor |
50 hp |
$2.50 |
$1.32 |
$8.44 |
$0.52 |
$12.78 |
0.42 |
$1.50 |
$3.76 |
$5.87 |
Loader Tractor |
75 hp |
$3.75 |
$1.52 |
$7.49 |
$0.46 |
$13.21 |
0.55 |
$2.90 |
$4.37 |
$7.27 |
Swather |
12 ft |
$2.89 |
$7.96 |
$31.06 |
$1.82 |
$43.73 |
0.25 |
$2.71 |
$8.22 |
$10.93 |
Bale Accumulator |
|
$0.00 |
$0.38 |
$3.52 |
$0.21 |
$4.10 |
0.14 |
$0.05 |
$0.52 |
$0.57 |
Baler |
|
$0.00 |
$4.40 |
$18.08 |
$0.99 |
$23.47 |
0.25 |
$1.10 |
$4.77 |
$5.87 |
Farmhand Loader |
|
$0.00 |
$0.64 |
$2.27 |
$0.15 |
$3.06 |
0.30 |
$0.19 |
$0.73 |
$0.92 |
Harrow |
10 ft |
$0.00 |
$0.14 |
$1.68 |
$0.11 |
$2.12 |
0.11 |
$0.02 |
$0.22 |
$0.24 |
Hay Wagon |
|
$0.00 |
$0.06 |
$4.69 |
$0.17 |
$4.92 |
0.30 |
$0.02 |
$1.46 |
$1.48 |
Side Delivery Rake |
10 ft |
$0.00 |
$1.06 |
$5.57 |
$0.31 |
$6.94 |
0.17 |
$0.18 |
$1.00 |
$1.18 |
Total |
|
|
|
|
|
|
|
$8.77 |
$25.04 |
$33.82 |
Table 5. Cow-calf costs and returns, 350 cow herd
Gross Income |
Weight Per Animal |
Unit of Measure |
Total Units |
Price/Cost Per Unit |
Total Value |
Value/Cost Per Head |
Your Ranch |
Cull Cows |
1000.00 |
lbs |
53.00 |
$0.48 |
$25,440.00 |
$72.69 |
|
Cull Bulls |
1550.00 |
lbs |
4.00 |
$0.65 |
$4,030.00 |
$11.51 |
|
Yearling Replacements |
850.00 |
lbs |
20.00 |
$0.80 |
$13,600.00 |
$38.86 |
|
Heifer Calves |
470.00 |
lbs |
79.00 |
$1.20 |
$44,556.00 |
$127.30 |
|
Steer Calves |
500.00 |
lbs |
152.00 |
$1.28 |
$97,280.00 |
$277.94 |
|
Total Income |
|
|
|
|
$184,906.00 |
$528.30 |
|
Operating Costs |
Unit of Measure |
Total Units |
Price/Cost Per Unit |
Total Value |
Value/Cost Per Head |
Your Ranch |
Grass Hay (Meadow Hay) |
Ton |
1035.00 |
$40.00 |
$41,400.00 |
$118.29 |
|
Grain |
Ton |
20.00 |
$115.00 |
$2,300.00 |
$6.57 |
|
Alfalfa Hay |
Ton |
259.26 |
$85.00 |
$22,037.10 |
$62.96 |
|
Federal Grazing (BLM) |
AUM |
3325.00 |
$1.43 |
$4,754.75 |
$13.59 |
|
Horse (Shoeing, Vet, Feed, etc.) |
Head |
8.00 |
$360.00 |
$2,880.00 |
$8.23 |
|
Veterinary/Medical |
Head |
350.00 |
$20.00 |
$7,000.00 |
$20.00 |
|
Marketing (Brand, Video, Commission) |
Head |
308.00 |
$11.96 |
$3,698.12 |
$10.57 |
|
Checkoff |
Head |
308.00 |
$1.00 |
$308.00 |
$0.88 |
|
Salt & Minerals |
Ton |
20.00 |
$261.00 |
$5,220.00 |
$14.91 |
|
Hauling |
$ |
732.00 |
$1.82 |
$1,332.24 |
$3.81 |
|
Hired Labor |
Days |
20.00 |
$100.00 |
$2,000.00 |
$5.71 |
|
Operator Labor |
Monthly |
12.00 |
$1,000.00 |
$12,000.00 |
$34.29 |
|
Accounting & Legal Fees |
$ |
1.00 |
$2,000.00 |
$2,000.00 |
$5.71 |
|
Maintenance (Buildings, Vehicles, etc.) |
$ |
1.00 |
$10,171.42 |
$10,171.42 |
$29.06 |
|
Fuel & Lube |
$ |
1.00 |
$6,587.90 |
$6,587.90 |
$18.82 |
|
Utilities |
$ |
1.00 |
$3,000.00 |
$3,000.00 |
$8.57 |
|
Miscellaneous |
Head |
350.00 |
$5.00 |
$1,750.00 |
$5.00 |
|
Interest Operating Capital |
$ |
$102,751.62 |
0.065 |
$3,339.43 |
$9.54 |
|
Total Operating Costs |
|
|
|
$131,778.96 |
$376.51 |
|
Income Above Operating Costs |
|
|
|
$53,127.04 |
$151.79 |
|
Ownership Costs (Capital Recovery (Depreciation) & Cash Overhead) |
Unit of Measure |
Total Units |
Price/Cost Per Unit |
Total Value |
Value/Cost Per Head |
Your Ranch |
Buildings, Improvements, & Equipment (Capital Recovery) |
$ |
1.00 |
$24,374.67 |
$24,374.67 |
$69.64 |
|
Machinery & Vehicles (Capital Recovery) |
$ |
1.00 |
$11,169.10 |
$11,169.10 |
$31.91 |
|
Purchased Livestock (Bulls & Horses) (Capital Recovery) |
$ |
1.00 |
$9,000.00 |
$9,000.00 |
$25.71 |
|
Liability Insurance (Cash Overhead) |
$ |
1.00 |
$1,749.00 |
$1,749.00 |
$5.00 |
|
Office & Travel (Cash Overhead) |
$ |
1.00 |
$3,000.00 |
$3,000.00 |
$8.57 |
|
Interest on Retained Livestock (Cash Overhead) |
$ |
1.00 |
$1,683.92 |
$1,683.92 |
$4.81 |
|
Annual Investment Insurance (Cash Overhead) |
$ |
1.00 |
$1,287.42 |
$1,287.42 |
$3.68 |
|
Annual Investment Taxes (Cash Overhead) |
$ |
1.00 |
$1,933.07 |
$1,933.07 |
$5.52 |
|
Total Ownership Costs |
|
|
|
$54,197.18 |
$154.85 |
|
Total Costs |
|
|
|
$185,976.14 |
$531.36 |
|
Net Projected Returns |
|
|
|
-$1,070.14 |
-$3.06 |
|